Ang teknolohiya ng wafer dicing, bilang isang kritikal na hakbang sa proseso ng pagmamanupaktura ng semiconductor, ay direktang nauugnay sa pagganap ng chip, ani, at mga gastos sa produksyon.
#01 Background at Kahalagahan ng Wafer Dicing
1.1 Kahulugan ng Wafer Dicing
Ang wafer dicing (kilala rin bilang scribing) ay isang mahalagang hakbang sa paggawa ng semiconductor, na naglalayong hatiin ang mga naprosesong wafer sa maraming indibidwal na dies. Ang mga dies na ito ay karaniwang naglalaman ng kumpletong pag-andar ng circuit at ang mga pangunahing bahagi na sa huli ay ginagamit sa paggawa ng mga elektronikong device. Habang nagiging mas kumplikado ang mga disenyo ng chip at patuloy na lumiliit ang mga sukat, ang mga kinakailangan sa katumpakan at kahusayan para sa teknolohiya ng wafer dicing ay nagiging mas mahigpit.
Sa mga praktikal na operasyon, ang wafer dicing ay karaniwang gumagamit ng mga tool na may mataas na katumpakan tulad ng mga diamond blades upang matiyak na ang bawat die ay nananatiling buo at ganap na gumagana. Kabilang sa mga pangunahing hakbang ang paghahanda bago ang pagputol, ang tumpak na kontrol sa panahon ng proseso ng pagputol, at ang kalidad ng inspeksyon pagkatapos ng pagputol.
Bago ang pagputol, ang wafer ay dapat na markahan at nakaposisyon upang matiyak ang tumpak na mga landas sa pagputol. Sa panahon ng pagputol, dapat na mahigpit na kontrolin ang mga parameter tulad ng presyon at bilis ng tool upang maiwasan ang pinsala sa wafer. Pagkatapos ng pagputol, ang mga komprehensibong inspeksyon sa kalidad ay isinasagawa upang matiyak na ang bawat chip ay nakakatugon sa mga pamantayan ng pagganap.
Ang mga pangunahing prinsipyo ng teknolohiya ng wafer dicing ay sumasaklaw hindi lamang sa pagpili ng mga kagamitan sa paggupit at ang pagtatakda ng mga parameter ng proseso kundi pati na rin ang impluwensya ng mga mekanikal na katangian at katangian ng mga materyales sa kalidad ng pagputol. Halimbawa, ang mga low-k na dielectric na silicon na wafer, dahil sa kanilang mababang mekanikal na katangian, ay lubhang madaling kapitan sa konsentrasyon ng stress sa panahon ng pagputol, na humahantong sa mga pagkabigo tulad ng pag-chip at pag-crack. Ang mababang tigas at brittleness ng mga low-k na materyales ay nagiging mas madaling kapitan ng pinsala sa istruktura sa ilalim ng mekanikal na puwersa o thermal stress, lalo na sa panahon ng pagputol. Ang pakikipag-ugnayan sa pagitan ng tool at ng wafer na ibabaw, kasama ng mataas na temperatura, ay maaaring lalong magpalala ng konsentrasyon ng stress.
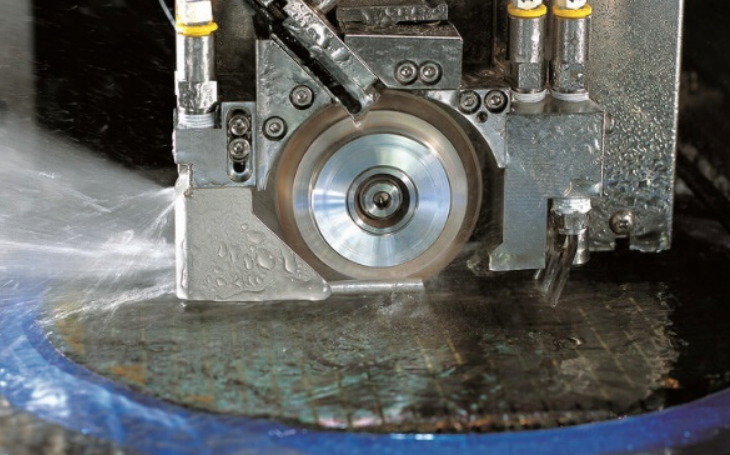
Sa mga pagsulong sa materyal na agham, lumawak ang teknolohiya ng wafer dicing nang higit pa sa tradisyonal na mga semiconductor na nakabatay sa silicon upang isama ang mga bagong materyales tulad ng gallium nitride (GaN). Ang mga bagong materyales na ito, dahil sa kanilang katigasan at mga katangian ng istruktura, ay nagdudulot ng mga bagong hamon para sa mga proseso ng dicing, na nangangailangan ng karagdagang pagpapabuti sa mga tool at diskarte sa pagputol.
Bilang isang kritikal na proseso sa industriya ng semiconductor, ang wafer dicing ay patuloy na ino-optimize bilang tugon sa mga umuusbong na pangangailangan at pagsulong sa teknolohiya, na naglalagay ng batayan para sa hinaharap na microelectronics at integrated circuit na mga teknolohiya.
Ang mga pagpapahusay sa teknolohiya ng wafer dicing ay higit pa sa pagbuo ng mga pantulong na materyales at kasangkapan. Sinasaklaw din nila ang pag-optimize ng proseso, mga pagpapahusay sa pagganap ng kagamitan, at tumpak na kontrol ng mga parameter ng dicing. Ang mga pagsulong na ito ay naglalayong tiyakin ang mataas na katumpakan, kahusayan, at katatagan sa proseso ng wafer dicing, na nakakatugon sa pangangailangan ng industriya ng semiconductor para sa mas maliliit na dimensyon, mas mataas na pagsasama, at mas kumplikadong mga istraktura ng chip.
Lugar ng pagpapabuti | Mga Tukoy na Panukala | Mga epekto |
Pag-optimize ng Proseso | - Pagbutihin ang mga paunang paghahanda, tulad ng mas tumpak na pagpoposisyon ng wafer at pagpaplano ng landas. | - Bawasan ang mga error sa pagputol at pagbutihin ang katatagan. |
- I-minimize ang mga error sa pagputol at pagbutihin ang katatagan. | - Magpatibay ng real-time na pagsubaybay at mga mekanismo ng feedback upang ayusin ang presyon, bilis, at temperatura ng tool. | |
- Ibaba ang mga rate ng pagkasira ng wafer at pagbutihin ang kalidad ng chip. | ||
Pagpapahusay ng Pagganap ng Kagamitan | - Gumamit ng mga high-precision na mekanikal na sistema at advanced na teknolohiya sa pagkontrol ng automation. | - Pahusayin ang katumpakan ng pagputol at bawasan ang pag-aaksaya ng materyal. |
- Ipakilala ang teknolohiya ng laser cutting na angkop para sa mga wafer na may mataas na tigas na materyal. | - Pagbutihin ang kahusayan sa produksyon at bawasan ang mga manu-manong error. | |
- Palakihin ang automation ng kagamitan para sa awtomatikong pagsubaybay at pagsasaayos. | ||
Tumpak na Parameter Control | - Pinong ayusin ang mga parameter tulad ng lalim ng pagputol, bilis, uri ng tool, at mga paraan ng paglamig. | - Tiyakin ang integridad ng die at pagganap ng kuryente. |
- I-customize ang mga parameter batay sa materyal na wafer, kapal, at istraktura. | - Palakasin ang mga rate ng ani, bawasan ang materyal na basura, at babaan ang mga gastos sa produksyon. | |
Estratehikong Kahalagahan | - Patuloy na galugarin ang mga bagong teknolohikal na landas, i-optimize ang mga proseso, at pahusayin ang mga kakayahan ng kagamitan upang matugunan ang mga pangangailangan sa merkado. | - Pagbutihin ang ani at pagganap ng paggawa ng chip, na sumusuporta sa pagbuo ng mga bagong materyales at mga advanced na disenyo ng chip. |
1.2 Ang Kahalagahan ng Wafer Dicing
Ang wafer dicing ay gumaganap ng isang kritikal na papel sa proseso ng pagmamanupaktura ng semiconductor, na direktang nakakaapekto sa mga susunod na hakbang pati na rin ang kalidad at pagganap ng huling produkto. Ang kahalagahan nito ay maaaring detalyado tulad ng sumusunod:
Una, ang katumpakan at pagkakapare-pareho ng dicing ay susi sa pagtiyak ng ani at pagiging maaasahan ng chip. Sa panahon ng pagmamanupaktura, ang mga wafer ay sumasailalim sa maraming hakbang sa pagpoproseso upang bumuo ng maraming masalimuot na istruktura ng circuit, na dapat na tiyak na nahahati sa mga indibidwal na chips (dies). Kung may mga makabuluhang error sa alignment o pagputol sa panahon ng proseso ng dicing, maaaring masira ang mga circuit, na makakaapekto sa functionality at reliability ng chip. Samakatuwid, hindi lamang tinitiyak ng high-precision dicing na teknolohiya ang integridad ng bawat chip ngunit pinipigilan din ang pinsala sa mga panloob na circuit, na pinapabuti ang kabuuang rate ng ani.
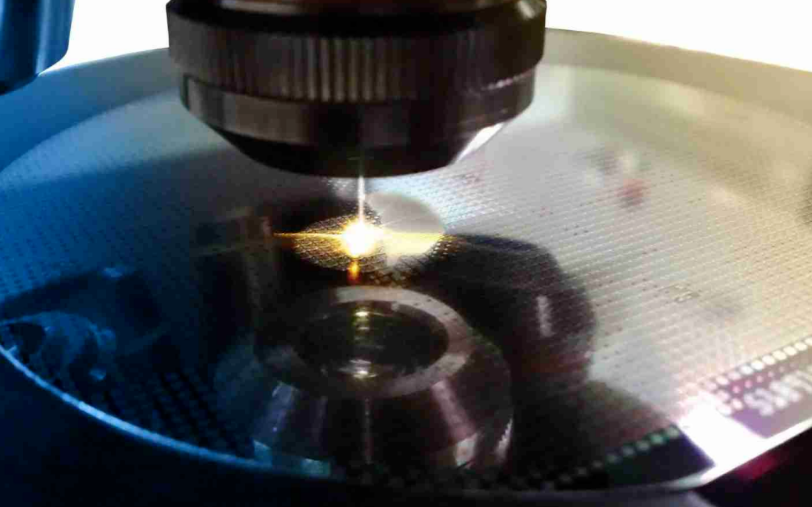
Pangalawa, ang wafer dicing ay may malaking epekto sa kahusayan ng produksyon at kontrol sa gastos. Bilang isang mahalagang hakbang sa proseso ng pagmamanupaktura, ang kahusayan nito ay direktang nakakaapekto sa pag-unlad ng mga kasunod na hakbang. Sa pamamagitan ng pag-optimize sa proseso ng dicing, pagtaas ng mga antas ng automation, at pagpapabuti ng mga bilis ng pagputol, ang pangkalahatang kahusayan sa produksyon ay maaaring lubos na mapahusay.
Sa kabilang banda, ang pag-aaksaya ng materyal sa panahon ng dicing ay isang kritikal na kadahilanan sa pamamahala ng gastos. Ang paggamit ng mga advanced na teknolohiya ng dicing ay hindi lamang binabawasan ang mga hindi kinakailangang pagkalugi ng materyal sa panahon ng proseso ng pagputol ngunit pinapataas din ang paggamit ng wafer, sa gayon ay nagpapababa ng mga gastos sa produksyon.
Sa mga pagsulong sa teknolohiyang semiconductor, patuloy na tumataas ang mga diameter ng wafer, at ang mga density ng circuit ay tumataas nang naaayon, na naglalagay ng mas mataas na pangangailangan sa teknolohiya ng dicing. Ang mga malalaking wafer ay nangangailangan ng mas tumpak na kontrol sa mga daanan ng pagputol, lalo na sa mga lugar na may mataas na density, kung saan kahit na ang mga maliliit na paglihis ay maaaring magdulot ng maraming chips na may sira. Bukod pa rito, ang mga malalaking wafer ay nagsasangkot ng higit pang mga linya ng pagputol at mas kumplikadong mga hakbang sa proseso, na nangangailangan ng higit pang mga pagpapabuti sa katumpakan, pagkakapare-pareho, at kahusayan ng mga teknolohiya ng dicing upang matugunan ang mga hamong ito.
1.3 Proseso ng Wafer Dicing
Ang proseso ng wafer dicing ay sumasaklaw sa lahat ng mga hakbang mula sa yugto ng paghahanda hanggang sa huling inspeksyon ng kalidad, na ang bawat yugto ay kritikal sa pagtiyak ng kalidad at pagganap ng mga diced chips. Nasa ibaba ang isang detalyadong paliwanag ng bawat yugto.
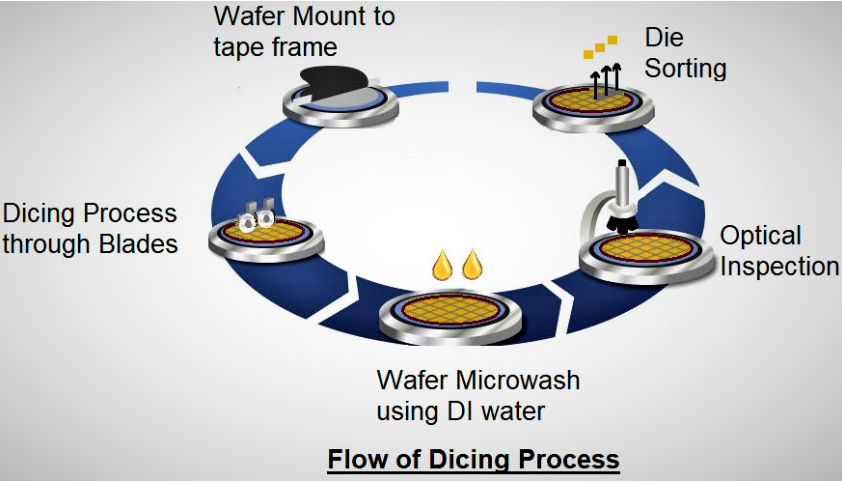
Phase | Detalyadong Paglalarawan |
Yugto ng Paghahanda | -Paglilinis ng Wafer: Gumamit ng tubig na may mataas na kadalisayan at mga espesyal na ahente ng paglilinis, na sinamahan ng ultrasonic o mekanikal na pagkayod, upang alisin ang mga dumi, particle, at contaminants, na tinitiyak ang isang malinis na ibabaw. -Tumpak na Pagpoposisyon: Gumamit ng high-precision na kagamitan upang matiyak na ang wafer ay tumpak na nahahati sa mga idinisenyong cutting path. -Pag-aayos ng Wafer: I-secure ang wafer sa isang tape frame upang mapanatili ang katatagan sa panahon ng pagputol, maiwasan ang pinsala mula sa vibration o paggalaw. |
Phase ng Pagputol | -Blade Dicing: Gumamit ng high-speed rotating diamond-coated blades para sa pisikal na pagputol, na angkop para sa silicon-based na materyales at cost-effective. -Laser Dicing: Gumamit ng mga high-energy laser beam para sa non-contact cutting, perpekto para sa malutong o mataas na tigas na materyales tulad ng gallium nitride, na nag-aalok ng mas mataas na katumpakan at mas kaunting pagkawala ng materyal. -Mga Bagong Teknolohiya: Ipakilala ang mga teknolohiya sa pagputol ng laser at plasma upang higit na mapabuti ang kahusayan at katumpakan habang pinapaliit ang mga zone na apektado ng init. |
Yugto ng Paglilinis | - Gumamit ng deionized water (DI water) at mga espesyal na ahente ng paglilinis, na sinamahan ng ultrasonic o spray na paglilinis, upang alisin ang mga labi at alikabok na nabuo sa panahon ng pagputol, na pumipigil sa mga nalalabi na makaapekto sa mga kasunod na proseso o chip electrical performance. - Iniiwasan ng high-purity na tubig ng DI ang pagpasok ng mga bagong contaminant, na tinitiyak ang isang malinis na kapaligiran ng wafer. |
Yugto ng Inspeksyon | -Optical Inspection: Gumamit ng mga optical detection system na sinamahan ng mga algorithm ng AI upang mabilis na matukoy ang mga depekto, tiyaking walang mga bitak o chipping sa mga diced chips, pagpapabuti ng kahusayan sa inspeksyon, at bawasan ang error ng tao. -Pagsukat ng Dimensyon: I-verify na ang mga sukat ng chip ay nakakatugon sa mga detalye ng disenyo. -Pagsubok sa Pagganap ng Elektrisidad: Tiyakin na ang pagganap ng kuryente ng mga kritikal na chip ay nakakatugon sa mga pamantayan, na ginagarantiyahan ang pagiging maaasahan sa mga susunod na aplikasyon. |
Yugto ng Pag-uuri | - Gumamit ng mga robotic arm o vacuum suction cup para paghiwalayin ang mga kuwalipikadong chips mula sa tape frame at awtomatikong pag-uri-uriin ang mga ito batay sa performance, tinitiyak ang kahusayan at flexibility ng produksyon habang pinapabuti ang katumpakan. |
Ang proseso ng pagputol ng wafer ay nagsasangkot ng paglilinis ng wafer, pagpoposisyon, pagputol, paglilinis, inspeksyon, at pag-uuri, na ang bawat hakbang ay kritikal. Sa mga pagsulong sa automation, laser cutting, at AI inspection technologies, ang mga modernong wafer cutting system ay makakamit ang mas mataas na katumpakan, bilis, at mas mababang pagkawala ng materyal. Sa hinaharap, ang mga bagong teknolohiya sa pagputol tulad ng laser at plasma ay unti-unting papalitan ang tradisyonal na pagputol ng talim upang matugunan ang mga pangangailangan ng lalong kumplikadong mga disenyo ng chip, na higit na nagtutulak sa pagbuo ng mga proseso ng pagmamanupaktura ng semiconductor.
Teknolohiya sa Pagputol ng Wafer at Mga Prinsipyo Nito
Ang larawan ay naglalarawan ng tatlong karaniwang mga teknolohiya sa pagputol ng ostiya:Blade Dicing,Laser Dicing, atPlasma Dicing. Nasa ibaba ang isang detalyadong pagsusuri at karagdagang paliwanag sa tatlong pamamaraang ito:
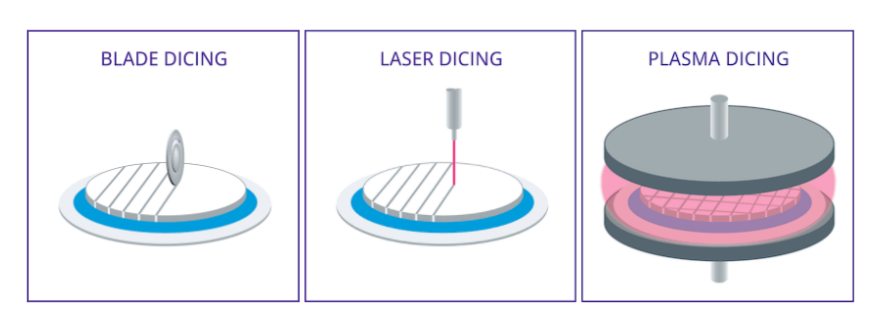
Sa paggawa ng semiconductor, ang pagputol ng wafer ay isang mahalagang hakbang na nangangailangan ng pagpili ng naaangkop na paraan ng pagputol batay sa kapal ng wafer. Ang unang hakbang ay upang matukoy ang kapal ng wafer. Kung ang kapal ng wafer ay lumampas sa 100 microns, maaaring piliin ang blade dicing bilang paraan ng pagputol. Kung hindi angkop ang blade dicing, maaaring gamitin ang fracture dicing method, na kinabibilangan ng parehong scribe cutting at blade dicing techniques.
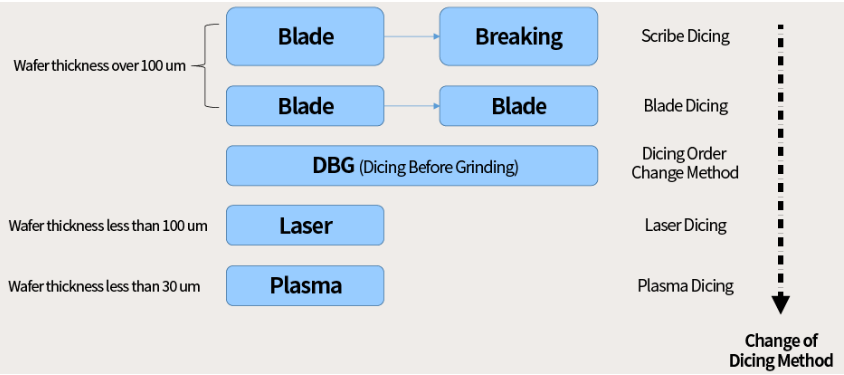
Kapag ang kapal ng wafer ay nasa pagitan ng 30 at 100 microns, inirerekomenda ang paraan ng DBG (Dice Before Grinding). Sa kasong ito, maaaring piliin ang scribe cutting, blade dicing, o pagsasaayos ng cutting sequence kung kinakailangan upang makamit ang pinakamahusay na mga resulta.
Para sa mga ultra-manipis na mga wafer na may kapal na mas mababa sa 30 microns, ang laser cutting ay nagiging ang ginustong paraan dahil sa kakayahan nitong i-cut ang manipis na mga wafer nang tumpak nang hindi nagdudulot ng labis na pinsala. Kung hindi matugunan ng laser cutting ang mga partikular na pangangailangan, ang pagputol ng plasma ay maaaring gamitin bilang alternatibo. Ang flowchart na ito ay nagbibigay ng malinaw na landas sa paggawa ng desisyon upang matiyak na ang pinaka-angkop na teknolohiya sa pagputol ng wafer ay pipiliin sa ilalim ng iba't ibang kondisyon ng kapal.
2.1 Teknolohiya ng Mechanical Cutting
Ang mekanikal na teknolohiya sa pagputol ay ang tradisyonal na pamamaraan sa wafer dicing. Ang pangunahing prinsipyo ay ang paggamit ng isang high-speed rotating diamond grinding wheel bilang isang cutting tool upang hatiin ang wafer. Ang mga pangunahing kagamitan ay may kasamang air-bearing spindle, na nagtutulak sa diamond grinding wheel tool sa mataas na bilis upang magsagawa ng tumpak na pagputol o pag-ukit sa isang paunang natukoy na daanan ng pagputol. Ang teknolohiyang ito ay malawakang ginagamit sa industriya dahil sa mababang gastos, mataas na kahusayan, at malawak na kakayahang magamit.
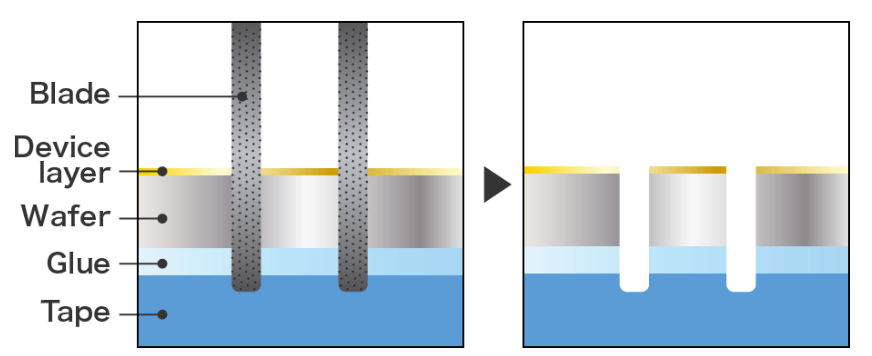
Mga kalamangan
Ang mataas na tigas at wear resistance ng mga tool sa paggiling ng brilyante ay nagbibigay-daan sa teknolohiya ng mekanikal na pagputol na umangkop sa mga pangangailangan sa pagputol ng iba't ibang mga materyales na wafer, kung tradisyunal na materyales na nakabatay sa silicon o mas bagong compound semiconductors. Ang operasyon nito ay simple, na may medyo mababang teknikal na mga kinakailangan, higit pang nagtataguyod ng katanyagan nito sa mass production. Bukod pa rito, kumpara sa iba pang mga paraan ng pagputol tulad ng laser cutting, ang mekanikal na pagputol ay may mas nakokontrol na mga gastos, na ginagawa itong angkop para sa mataas na dami ng mga pangangailangan sa produksyon.
Mga Limitasyon
Sa kabila ng maraming pakinabang nito, may mga limitasyon din ang mechanical cutting technology. Una, dahil sa pisikal na pakikipag-ugnayan sa pagitan ng tool at ng wafer, ang katumpakan ng pagputol ay medyo limitado, kadalasang humahantong sa mga dimensional deviations na maaaring makaapekto sa katumpakan ng kasunod na chip packaging at pagsubok. Pangalawa, ang mga depekto tulad ng chipping at crack ay madaling mangyari sa panahon ng mekanikal na proseso ng pagputol, na hindi lamang nakakaapekto sa yield rate ngunit maaari ring negatibong makaapekto sa pagiging maaasahan at habang-buhay ng chips. Ang pinsalang dulot ng mekanikal na stress ay partikular na nakapipinsala para sa paggawa ng high-density na chip, lalo na kapag pinuputol ang mga malutong na materyales, kung saan mas kitang-kita ang mga isyung ito.
Teknolohikal na Pagpapabuti
Upang malampasan ang mga limitasyong ito, patuloy na ino-optimize ng mga mananaliksik ang mekanikal na proseso ng pagputol. Kabilang sa mga pangunahing pagpapahusay ang pagpapahusay sa disenyo at pagpili ng materyal ng mga grinding wheel upang mapabuti ang katumpakan at tibay ng pagputol. Bukod pa rito, ang pag-optimize ng istrukturang disenyo at mga sistema ng kontrol ng mga kagamitan sa paggupit ay lalong nagpabuti sa katatagan at automation ng proseso ng pagputol. Binabawasan ng mga pagsulong na ito ang mga error na dulot ng mga operasyon ng tao at pinapabuti ang pagkakapare-pareho ng mga pagbawas. Ang pagpapakilala ng mga advanced na inspeksyon at mga teknolohiya sa pagkontrol ng kalidad para sa real-time na pagsubaybay ng mga anomalya sa panahon ng proseso ng pagputol ay makabuluhang napabuti din ang pagiging maaasahan at ani ng pagputol.
Pag-unlad sa Hinaharap at Mga Bagong Teknolohiya
Bagama't ang teknolohiya ng mekanikal na pagputol ay may malaking posisyon pa rin sa pagputol ng wafer, ang mga bagong teknolohiya sa pagputol ay mabilis na umuunlad habang umuusbong ang mga proseso ng semiconductor. Halimbawa, ang paggamit ng thermal laser cutting technology ay nagbibigay ng mga bagong solusyon sa mga isyu sa katumpakan at depekto sa mekanikal na pagputol. Binabawasan ng pamamaraang ito ng non-contact cutting ang pisikal na stress sa wafer, na makabuluhang nagpapababa sa insidente ng chipping at crack, lalo na kapag nagpuputol ng mas malutong na materyales. Sa hinaharap, ang pagsasanib ng mekanikal na teknolohiya sa pagputol sa mga umuusbong na pamamaraan ng pagputol ay magbibigay ng pagmamanupaktura ng semiconductor na may higit pang mga opsyon at flexibility, higit pang pagpapahusay ng kahusayan sa pagmamanupaktura at kalidad ng chip.
Sa konklusyon, kahit na ang mechanical cutting technology ay may ilang mga disbentaha, ang patuloy na teknolohikal na pagpapabuti at ang pagsasama nito sa mga bagong cutting technique ay nagbibigay-daan pa rin dito na gumanap ng mahalagang papel sa paggawa ng semiconductor at mapanatili ang pagiging mapagkumpitensya nito sa mga proseso sa hinaharap.
2.2 Laser Cutting Technology
Ang teknolohiya ng pagputol ng laser, bilang isang bagong paraan sa pagputol ng wafer, ay unti-unting nakakuha ng malawak na atensyon sa industriya ng semiconductor dahil sa mataas na katumpakan nito, kakulangan ng pinsala sa mekanikal na pakikipag-ugnay, at mabilis na mga kakayahan sa pagputol. Ginagamit ng teknolohiyang ito ang mataas na densidad ng enerhiya at kakayahang tumutok ng isang laser beam upang lumikha ng isang maliit na zone na apektado ng init sa ibabaw ng materyal na wafer. Kapag ang laser beam ay inilapat sa wafer, ang thermal stress na nabuo ay nagiging sanhi ng pagkabali ng materyal sa itinalagang lokasyon, na nakakamit ng tumpak na pagputol.
Mga Bentahe ng Laser Cutting Technology
• Mataas na Katumpakan: Ang tumpak na kakayahan sa pagpoposisyon ng laser beam ay nagbibigay-daan para sa micron o kahit nanometer-level cutting precision, na nakakatugon sa mga kinakailangan ng modernong high-precision, high-density integrated circuit manufacturing.
• Walang Mechanical Contact: Ang pagputol ng laser ay umiiwas sa pisikal na pakikipag-ugnayan sa wafer, na pumipigil sa mga karaniwang isyu sa mekanikal na pagputol, tulad ng pag-chip at pag-crack, na makabuluhang nagpapabuti sa rate ng ani at pagiging maaasahan ng mga chips.
• Mabilis na Bilis ng Pagputol: Ang mataas na bilis ng pagputol ng laser ay nag-aambag sa pagtaas ng kahusayan sa produksyon, na ginagawa itong lalong angkop para sa malakihan, mataas na bilis ng mga sitwasyon sa produksyon.
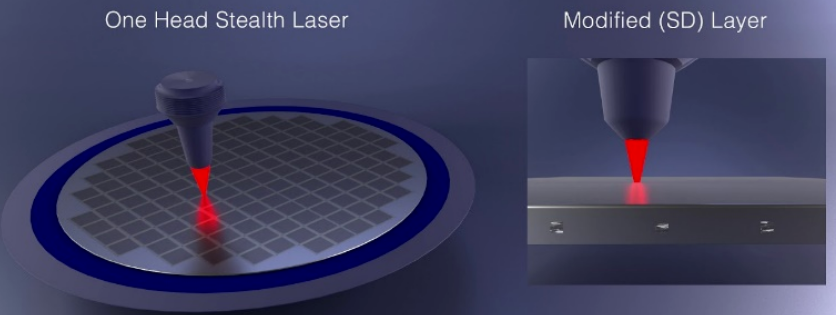
Mga Hamong Hinaharap
• Mataas na Gastos sa Kagamitan: Ang paunang pamumuhunan para sa laser cutting equipment ay mataas, na nagpapakita ng pang-ekonomiyang presyon, lalo na para sa maliit hanggang katamtamang laki ng mga negosyo sa produksyon.
• Kumplikadong Pagkontrol sa Proseso: Ang pagputol ng laser ay nangangailangan ng tumpak na kontrol ng ilang mga parameter, kabilang ang density ng enerhiya, posisyon ng focus, at bilis ng pagputol, na ginagawang kumplikado ang proseso.
• Mga Isyu sa Sona na Naaapektuhan ng init: Bagama't binabawasan ng non-contact na katangian ng laser cutting ang mekanikal na pinsala, ang thermal stress na dulot ng heat-affected zone (HAZ) ay maaaring negatibong makaapekto sa mga katangian ng wafer na materyal. Ang karagdagang pag-optimize ng proseso ay kailangan para mabawasan ang epektong ito.
Mga Direksyon sa Pagpapaunlad ng Teknolohikal
Upang matugunan ang mga hamong ito, ang mga mananaliksik ay tumutuon sa pagpapababa ng mga gastos sa kagamitan, pagpapabuti ng kahusayan sa pagputol, at pag-optimize ng daloy ng proseso.
• Mahusay na Laser at Optical System: Sa pamamagitan ng pagbuo ng mas mahusay na mga laser at advanced na optical system, posibleng mapababa ang mga gastos sa kagamitan habang pinapahusay ang katumpakan at bilis ng pagputol.
• Pag-optimize ng Mga Parameter ng Proseso: Ang malalim na pagsasaliksik sa pakikipag-ugnayan sa pagitan ng mga laser at wafer na materyales ay isinasagawa upang pahusayin ang mga prosesong nagpapababa sa lugar na apektado ng init, sa gayo'y nagpapabuti sa kalidad ng pagputol.
• Intelligent Control System: Ang pagbuo ng mga teknolohiyang matalinong kontrol ay naglalayong i-automate at i-optimize ang proseso ng pagputol ng laser, pagpapabuti ng katatagan at pagkakapare-pareho nito.
Ang teknolohiya ng laser cutting ay partikular na epektibo sa mga ultra-manipis na wafer at high-precision na mga senaryo ng pagputol. Habang tumataas ang laki ng wafer at tumataas ang mga densidad ng circuit, nagpupumilit ang tradisyonal na mekanikal na mga pamamaraan ng pagputol upang matugunan ang mataas na katumpakan at mataas na kahusayan na hinihingi ng modernong pagmamanupaktura ng semiconductor. Dahil sa mga natatanging bentahe nito, ang pagputol ng laser ay nagiging ginustong solusyon sa mga larangang ito.
Bagama't ang teknolohiya ng laser cutting ay nahaharap pa rin sa mga hamon tulad ng mataas na gastos sa kagamitan at pagiging kumplikado ng proseso, ang mga natatanging bentahe nito sa mataas na katumpakan at non-contact na pinsala ay ginagawa itong isang mahalagang direksyon para sa pag-unlad sa paggawa ng semiconductor. Habang patuloy na sumusulong ang teknolohiya ng laser at mga intelligent na sistema ng kontrol, inaasahang higit na mapapabuti ng laser cutting ang kahusayan at kalidad ng pagputol ng wafer, na nagtutulak sa patuloy na pag-unlad ng industriya ng semiconductor.
2.3 Teknolohiya sa Pagputol ng Plasma
Ang teknolohiya ng paggupit ng plasma, bilang isang umuusbong na paraan ng dicing ng wafer, ay nakakuha ng makabuluhang pansin sa mga nakaraang taon. Gumagamit ang teknolohiyang ito ng mga high-energy plasma beam para tumpak na maputol ang mga wafer sa pamamagitan ng pagkontrol sa enerhiya, bilis, at pag-cut path ng plasma beam, na nakakamit ng pinakamainam na resulta ng pagputol.
Prinsipyo ng Paggawa at Mga Kalamangan
Ang proseso ng pagputol ng plasma ay umaasa sa isang mataas na temperatura, mataas na enerhiya na plasma beam na nabuo ng kagamitan. Ang beam na ito ay maaaring magpainit ng materyal na wafer sa punto ng pagkatunaw o singaw nito sa napakaikling panahon, na nagbibigay-daan sa mabilis na pagputol. Kung ikukumpara sa tradisyunal na mekanikal o laser cutting, ang plasma cutting ay mas mabilis at gumagawa ng mas maliit na heat-affected zone, na epektibong binabawasan ang paglitaw ng mga bitak at pinsala sa panahon ng pagputol.
Sa mga praktikal na aplikasyon, ang teknolohiya ng pagputol ng plasma ay partikular na sanay sa paghawak ng mga wafer na may mga kumplikadong hugis. Ang high-energy, adjustable plasma beam nito ay madaling mag-cut ng hindi regular na hugis na mga wafer na may mataas na katumpakan. Samakatuwid, sa microelectronics manufacturing, lalo na sa customized at small-batch production ng high-end chips, ang teknolohiyang ito ay nagpapakita ng magandang pangako para sa malawakang paggamit.
Mga Hamon at Limitasyon
Sa kabila ng maraming pakinabang ng teknolohiya sa pagputol ng plasma, nahaharap din ito sa ilang mga hamon.
• Masalimuot na Proseso: Ang proseso ng pagputol ng plasma ay masalimuot at nangangailangan ng mataas na katumpakan na kagamitan at may karanasan na mga operator upang matiyakkatumpakan at katatagan sa pagputol.
• Pagkontrol at Kaligtasan sa Kapaligiran: Ang mataas na temperatura, mataas na enerhiya na katangian ng plasma beam ay nangangailangan ng mahigpit na kontrol sa kapaligiran at mga hakbang sa kaligtasan, na nagpapataas sa pagiging kumplikado at gastos ng pagpapatupad.
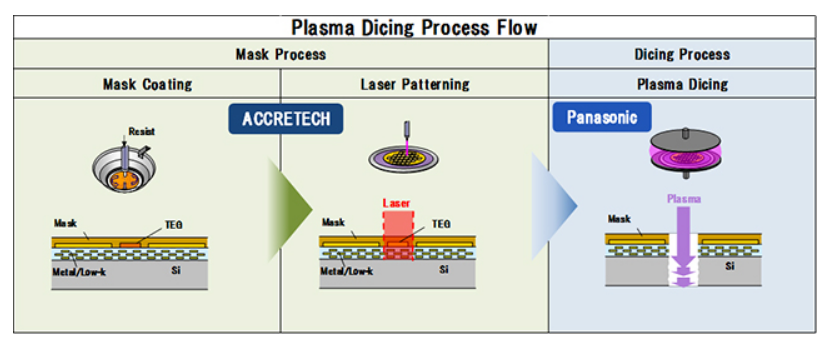
Mga Direksyon sa Pag-unlad sa Hinaharap
Sa pagsulong ng teknolohiya, ang mga hamon na nauugnay sa pagputol ng plasma ay inaasahang unti-unting malalampasan. Sa pamamagitan ng pagbuo ng mas matalino at mas matatag na kagamitan sa paggupit, ang pag-asa sa mga manu-manong operasyon ay maaaring mabawasan, sa gayon ay mapabuti ang kahusayan sa produksyon. Kasabay nito, ang pag-optimize ng mga parameter ng proseso at ang cutting environment ay makakatulong sa pagpapababa ng mga panganib sa kaligtasan at mga gastos sa pagpapatakbo.
Sa industriya ng semiconductor, ang mga inobasyon sa paggupit ng wafer at teknolohiya ng dicing ay mahalaga sa paghimok ng pag-unlad ng industriya. Ang teknolohiya sa pagputol ng plasma, na may mataas na katumpakan, kahusayan, at kakayahang pangasiwaan ang mga kumplikadong hugis ng wafer, ay lumitaw bilang isang makabuluhang bagong manlalaro sa larangang ito. Bagama't nananatili ang ilang hamon, unti-unting tutugunan ang mga isyung ito sa pamamagitan ng patuloy na pagbabago sa teknolohiya, na magdadala ng higit pang mga posibilidad at pagkakataon sa paggawa ng semiconductor.
Ang mga prospect ng aplikasyon ng teknolohiya ng pagputol ng plasma ay malawak, at inaasahang gaganap ito ng mas mahalagang papel sa paggawa ng semiconductor sa hinaharap. Sa pamamagitan ng tuluy-tuloy na teknolohikal na inobasyon at pag-optimize, ang pagputol ng plasma ay hindi lamang tutugon sa mga umiiral na hamon kundi maging isang makapangyarihang driver ng paglago ng industriya ng semiconductor.
2.4 Pagbawas ng Kalidad at Mga Salik na Nakakaimpluwensya
Ang kalidad ng pagputol ng wafer ay kritikal para sa kasunod na pag-package ng chip, pagsubok, at ang pangkalahatang pagganap at pagiging maaasahan ng huling produkto. Kasama sa mga karaniwang isyung nararanasan sa panahon ng pagputol ang mga bitak, pag-chipping, at mga paglihis sa pagputol. Ang mga problemang ito ay naiimpluwensyahan ng ilang salik na nagtutulungan.
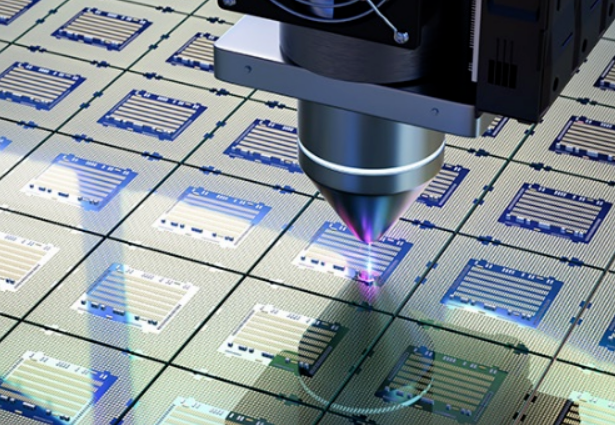
Kategorya | Nilalaman | Epekto |
Mga Parameter ng Proseso | Ang bilis ng pagputol, rate ng feed, at lalim ng pagputol ay direktang nakakaapekto sa katatagan at katumpakan ng proseso ng pagputol. Ang mga hindi tamang setting ay maaaring humantong sa konsentrasyon ng stress at sobrang init na apektadong zone, na nagreresulta sa mga bitak at chipping. Ang pagsasaayos ng mga parameter nang naaangkop batay sa materyal na wafer, kapal, at mga kinakailangan sa pagputol ay susi sa pagkamit ng ninanais na mga resulta ng pagputol. | Tinitiyak ng tamang mga parameter ng proseso ang tumpak na pagputol at binabawasan ang panganib ng mga depekto tulad ng mga bitak at chipping. |
Mga Salik ng Kagamitan at Materyal | -Kalidad ng talim: Ang materyal, tigas, at wear resistance ng blade ay nakakaimpluwensya sa kinis ng proseso ng pagputol at ang flatness ng cut surface. Ang mahinang kalidad na mga blades ay nagpapataas ng friction at thermal stress, na posibleng humantong sa mga bitak o chipping. Ang pagpili ng tamang materyal ng talim ay mahalaga. -Pagganap ng Coolant: Nakakatulong ang mga coolant na bawasan ang temperatura ng pagputol, bawasan ang friction, at i-clear ang mga debris. Ang hindi epektibong coolant ay maaaring humantong sa mataas na temperatura at pagtatayo ng mga labi, na nakakaapekto sa kalidad at kahusayan ng pagputol. Ang pagpili ng mahusay at environment friendly na mga coolant ay mahalaga. | Ang kalidad ng talim ay nakakaapekto sa katumpakan at kinis ng hiwa. Ang hindi epektibong coolant ay maaaring magresulta sa hindi magandang kalidad at kahusayan ng pagputol, na nagpapakita ng pangangailangan para sa pinakamainam na paggamit ng coolant. |
Kontrol sa Proseso at Pagsusuri ng Kalidad | -Kontrol sa Proseso: Real-time na pagsubaybay at pagsasaayos ng mga pangunahing parameter ng pagputol upang matiyak ang katatagan at pagkakapare-pareho sa proseso ng pagputol. -Quality Inspection: Ang mga pagsusuri sa hitsura pagkatapos ng pagputol, mga sukat ng dimensyon, at pagsusuri sa pagganap ng kuryente ay nakakatulong na matukoy at matugunan kaagad ang mga isyu sa kalidad, na pagpapabuti ng katumpakan at pagkakapare-pareho ng pagputol. | Nakakatulong ang wastong kontrol sa proseso at inspeksyon ng kalidad na matiyak ang pare-pareho, mataas na kalidad na mga resulta ng pagputol at maagang pagtuklas ng mga potensyal na isyu. |

Pagpapabuti ng Kalidad ng Pagputol
Ang pagpapabuti ng kalidad ng pagputol ay nangangailangan ng isang komprehensibong diskarte na isinasaalang-alang ang mga parameter ng proseso, pagpili ng kagamitan at materyal, kontrol sa proseso, at inspeksyon. Sa pamamagitan ng patuloy na pagpino sa mga teknolohiya ng pagputol at pag-optimize ng mga pamamaraan ng proseso, ang katumpakan at katatagan ng pagputol ng wafer ay maaaring higit na mapahusay, na nagbibigay ng mas maaasahang teknikal na suporta para sa industriya ng pagmamanupaktura ng semiconductor.
#03 Paghawak at Pagsubok sa Post-Cutting
3.1 Paglilinis at Pagpapatuyo
Ang mga hakbang sa paglilinis at pagpapatuyo pagkatapos ng pagputol ng wafer ay kritikal para matiyak ang kalidad ng chip at ang maayos na pag-unlad ng mga kasunod na proseso. Sa yugtong ito, mahalaga na masusing alisin ang mga labi ng silikon, nalalabi ng coolant, at iba pang mga kontaminant na nabuo sa panahon ng pagputol. Mahalaga rin na tiyakin na ang mga chips ay hindi nasira sa panahon ng proseso ng paglilinis, at pagkatapos ng pagpapatuyo, tiyaking walang kahalumigmigan na nananatili sa ibabaw ng chip upang maiwasan ang mga isyu tulad ng kaagnasan o electrostatic discharge.
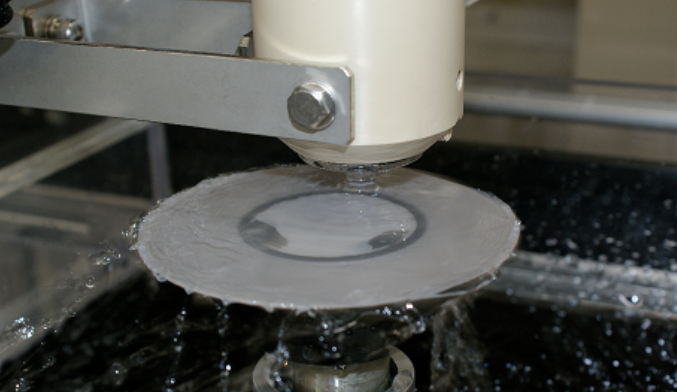
Post-Cutting Handling: Proseso ng Paglilinis at Pagpapatuyo
Hakbang ng Proseso | Nilalaman | Epekto |
Proseso ng Paglilinis | -Pamamaraan: Gumamit ng mga espesyal na ahente sa paglilinis at purong tubig, na sinamahan ng ultrasonic o mechanical brushing techniques para sa paglilinis. | Tinitiyak ang masusing pag-alis ng mga kontaminant at pinipigilan ang pinsala sa mga chips sa panahon ng paglilinis. |
-Pagpili ng Ahente ng Paglilinis: Pumili batay sa materyal na wafer at uri ng contaminant upang matiyak ang epektibong paglilinis nang hindi nasisira ang chip. | Ang tamang pagpili ng ahente ay susi para sa epektibong paglilinis at proteksyon ng chip. | |
-Kontrol ng Parameter: Mahigpit na kontrolin ang temperatura ng paglilinis, oras, at konsentrasyon ng solusyon sa paglilinis upang maiwasan ang mga isyu sa kalidad na dulot ng hindi tamang paglilinis. | Tumutulong ang mga kontrol upang maiwasang masira ang wafer o mag-iwan ng mga contaminant, na tinitiyak ang pare-parehong kalidad. | |
Proseso ng Pagpapatuyo | -Mga Tradisyunal na Pamamaraan: Natural na air drying at hot air drying, na may mababang kahusayan at maaaring humantong sa static na pagtitipon ng kuryente. | Maaaring magresulta sa mas mabagal na oras ng pagpapatuyo at mga potensyal na static na isyu. |
-Makabagong Teknolohiya: Gumamit ng mga advanced na teknolohiya tulad ng vacuum drying at infrared drying upang matiyak na mabilis matuyo ang mga chips at maiwasan ang mga nakakapinsalang epekto. | Mas mabilis at mas mahusay na proseso ng pagpapatuyo, binabawasan ang panganib ng static discharge o mga isyu na nauugnay sa moisture. | |
Pagpili at Pagpapanatili ng Kagamitan | -Pagpili ng Kagamitan: Ang mga makinang panglinis at pagpapatuyo na may mataas na pagganap ay nagpapabuti sa kahusayan sa pagpoproseso at pinong kontrolin ang mga potensyal na isyu sa panahon ng paghawak. | Tinitiyak ng mga de-kalidad na makina ang mas mahusay na pagproseso at binabawasan ang posibilidad ng mga pagkakamali sa panahon ng paglilinis at pagpapatuyo. |
-Pagpapanatili ng Kagamitan: Ang regular na inspeksyon at pagpapanatili ng mga kagamitan ay tinitiyak na nananatili ito sa pinakamainam na kondisyon sa pagtatrabaho, na ginagarantiyahan ang kalidad ng chip. | Pinipigilan ng wastong pagpapanatili ang mga pagkabigo ng kagamitan, tinitiyak ang maaasahan at mataas na kalidad na pagproseso. |
Paglilinis at Pagpatuyo Pagkatapos ng Pagputol
Ang mga hakbang sa paglilinis at pagpapatuyo pagkatapos ng pagputol ng wafer ay masalimuot at maselan na proseso na nangangailangan ng maingat na pagsasaalang-alang ng maraming salik upang matiyak ang panghuling resulta ng pagproseso. Sa pamamagitan ng paggamit ng mga siyentipikong pamamaraan at mahigpit na pamamaraan, posible na matiyak na ang bawat chip ay pumapasok sa kasunod na mga yugto ng packaging at pagsubok sa pinakamainam na kondisyon.
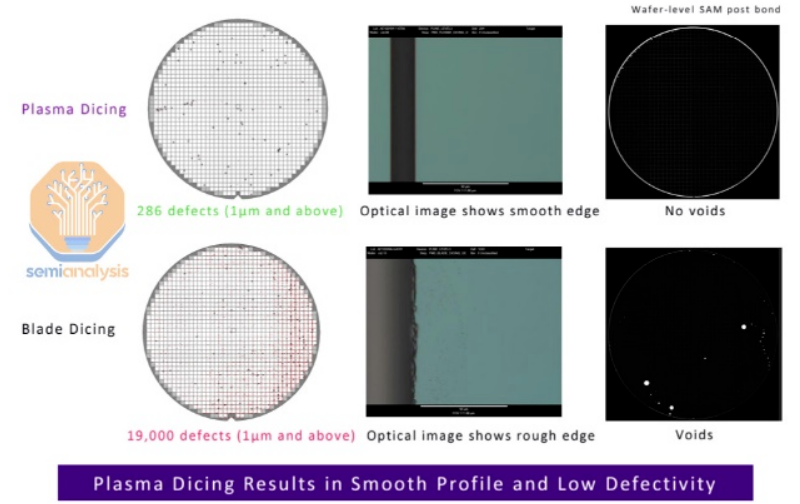
Post-Cutting Inspeksyon at Pagsubok
Hakbang | Nilalaman | Epekto |
Hakbang ng Inspeksyon | 1.Visual na Inspeksyon: Gumamit ng visual o automated na kagamitan sa inspeksyon upang suriin kung may nakikitang mga depekto tulad ng mga bitak, chipping, o kontaminasyon sa ibabaw ng chip. Mabilis na tukuyin ang mga pisikal na napinsalang chips upang maiwasan ang basura. | Tumutulong sa pagtukoy at pag-aalis ng mga may sira na chips nang maaga sa proseso, na binabawasan ang pagkawala ng materyal. |
2.Sukat ng Pagsukat: Gumamit ng mga aparato sa pagsukat ng katumpakan upang tumpak na sukatin ang mga sukat ng chip, tinitiyak na ang laki ng hiwa ay nakakatugon sa mga detalye ng disenyo at pinipigilan ang mga isyu sa pagganap o mga kahirapan sa packaging. | Tinitiyak na ang mga chip ay nasa loob ng mga kinakailangang limitasyon sa laki, na pumipigil sa pagkasira ng pagganap o mga problema sa pagpupulong. | |
3.Pagsubok sa Pagganap ng Elektrisidad: Suriin ang mga pangunahing parameter ng kuryente tulad ng resistensya, kapasidad, at inductance, upang matukoy ang mga hindi sumusunod na chip at matiyak na ang mga chip na kwalipikado lamang sa pagganap ang magpapatuloy sa susunod na yugto. | Tinitiyak na ang functional at performance-tested na chips lang ang sumusulong sa proseso, na binabawasan ang panganib ng pagkabigo sa mga susunod na yugto. | |
Hakbang sa Pagsubok | 1.Functional na Pagsubok: I-verify na gumagana ang pangunahing pag-andar ng chip ayon sa nilalayon, pagtukoy at pag-aalis ng mga chip na may mga abnormalidad sa paggana. | Tinitiyak na ang mga chip ay nakakatugon sa mga pangunahing kinakailangan sa pagpapatakbo bago umunlad sa mga susunod na yugto. |
2.Pagsubok sa pagiging maaasahan: Suriin ang katatagan ng pagganap ng chip sa ilalim ng matagal na paggamit o malupit na kapaligiran, na kadalasang kinasasangkutan ng mataas na temperatura ng pagtanda, mababang temperatura na pagsubok, at halumigmig na pagsubok upang gayahin ang totoong-world na matinding mga kondisyon. | Tinitiyak na ang mga chip ay mapagkakatiwalaang gumana sa ilalim ng hanay ng mga kondisyon sa kapaligiran, pagpapabuti ng mahabang buhay at katatagan ng produkto. | |
3.Pagsubok sa Pagkatugma: I-verify na gumagana nang maayos ang chip sa iba pang mga bahagi o system, na tinitiyak na walang mga pagkakamali o pagkasira ng pagganap dahil sa hindi pagkakatugma. | Tinitiyak ang maayos na operasyon sa mga real-world na application sa pamamagitan ng pagpigil sa mga isyu sa compatibility. |
3.3 Pag-iimbak at Pag-iimbak
Pagkatapos ng pagputol ng wafer, ang mga chips ay isang mahalagang output ng proseso ng pagmamanupaktura ng semiconductor, at ang kanilang mga yugto ng packaging at imbakan ay pantay na mahalaga. Ang wastong mga hakbang sa pag-iimbak at pag-iimbak ay mahalaga hindi lamang para sa pagtiyak ng kaligtasan at katatagan ng mga chips sa panahon ng transportasyon at pag-iimbak ngunit para din sa pagbibigay ng malakas na suporta para sa mga susunod na yugto ng produksyon, pagsubok, at packaging.
Buod ng mga Yugto ng Inspeksyon at Pagsubok:
Ang mga hakbang sa inspeksyon at pagsubok para sa mga chips pagkatapos ng pagputol ng wafer ay sumasaklaw sa isang hanay ng mga aspeto, kabilang ang visual na inspeksyon, pagsukat ng laki, pagsubok sa pagganap ng kuryente, pagsubok sa pagganap, pagsubok sa pagiging maaasahan, at pagsubok sa pagiging tugma. Ang mga hakbang na ito ay magkakaugnay at magkakaugnay, na bumubuo ng isang matatag na hadlang upang matiyak ang kalidad at pagiging maaasahan ng produkto. Sa pamamagitan ng mahigpit na inspeksyon at mga pamamaraan sa pagsubok, ang mga potensyal na isyu ay maaaring matukoy at malutas kaagad, na tinitiyak na ang panghuling produkto ay nakakatugon sa mga kinakailangan at inaasahan ng customer.
Aspeto | Nilalaman |
Mga Panukala sa Pag-iimpake | 1.Anti-static: Ang mga materyales sa packaging ay dapat magkaroon ng mahusay na anti-static na mga katangian upang maiwasan ang static na kuryente na makapinsala sa mga aparato o makaapekto sa kanilang pagganap. |
2.Moisture-proof: Ang mga materyales sa pag-iimpake ay dapat magkaroon ng magandang moisture resistance upang maiwasan ang kaagnasan at pagkasira ng pagganap ng kuryente na dulot ng halumigmig. | |
3.Shockproof: Ang mga materyales sa packaging ay dapat magbigay ng epektibong shock absorption upang maprotektahan ang mga chips mula sa panginginig ng boses at epekto sa panahon ng transportasyon. | |
Kapaligiran sa Imbakan | 1.Kontrol ng Halumigmig: Mahigpit na kontrolin ang halumigmig sa loob ng naaangkop na hanay upang maiwasan ang pagsipsip ng moisture at kaagnasan na dulot ng labis na halumigmig o mga static na isyu na dulot ng mababang kahalumigmigan. |
2.Kalinisan: Panatilihin ang isang malinis na kapaligiran sa imbakan upang maiwasan ang kontaminasyon ng mga chips ng alikabok at mga dumi. | |
3.Pagkontrol sa Temperatura: Magtakda ng makatwirang hanay ng temperatura at mapanatili ang katatagan ng temperatura upang maiwasan ang pinabilis na pagtanda dahil sa sobrang init o mga problema sa condensation na dulot ng mababang temperatura. | |
Regular na Inspeksyon | Regular na siyasatin at suriin ang mga nakaimbak na chip, gamit ang mga visual na inspeksyon, sukat ng sukat, at mga pagsubok sa pagganap ng kuryente upang matukoy at matugunan ang mga potensyal na isyu sa isang napapanahong paraan. Batay sa oras at kundisyon ng pag-iimbak, planuhin ang paggamit ng mga chips upang matiyak na ginagamit ang mga ito sa pinakamainam na kondisyon. |
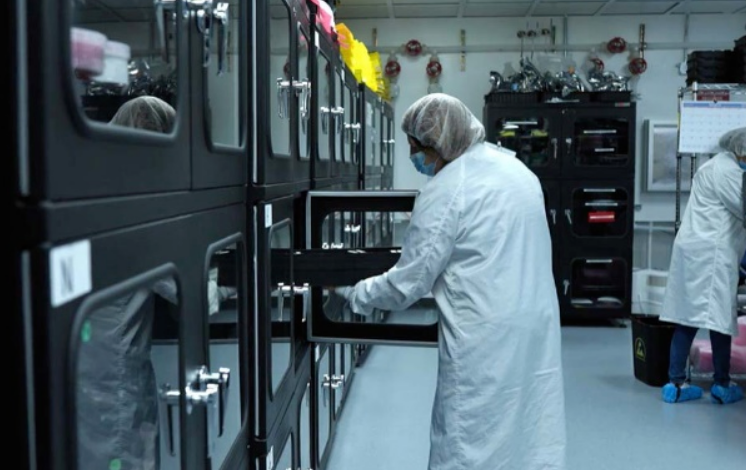
Ang isyu ng microcracks at pinsala sa panahon ng proseso ng wafer dicing ay isang malaking hamon sa paggawa ng semiconductor. Ang pagputol ng stress ay ang pangunahing sanhi ng hindi pangkaraniwang bagay na ito, dahil lumilikha ito ng maliliit na bitak at pinsala sa ibabaw ng wafer, na humahantong sa pagtaas ng mga gastos sa pagmamanupaktura at pagbaba sa kalidad ng produkto.
Upang matugunan ang hamon na ito, napakahalagang bawasan ang stress sa pagputol at ipatupad ang mga naka-optimize na diskarte sa paggupit, kasangkapan, at kundisyon. Ang maingat na pansin sa mga kadahilanan tulad ng materyal ng talim, bilis ng pagputol, presyon, at mga paraan ng paglamig ay maaaring makatulong na mabawasan ang pagbuo ng mga microcrack at mapabuti ang pangkalahatang ani ng proseso. Bukod pa rito, ang patuloy na pagsasaliksik sa mga mas advanced na teknolohiya sa pagputol, tulad ng laser dicing, ay tumitingin ng mga paraan upang higit pang mapagaan ang mga isyung ito.
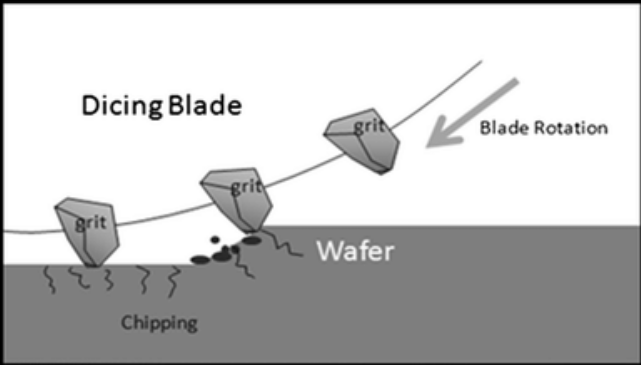
Bilang isang marupok na materyal, ang mga wafer ay madaling kapitan ng mga panloob na pagbabago sa istruktura kapag sumasailalim sa mekanikal, thermal, o kemikal na stress, na humahantong sa pagbuo ng mga microcrack. Bagama't ang mga bitak na ito ay maaaring hindi agad na mapapansin, maaari itong lumawak at magdulot ng mas matinding pinsala habang umuusad ang proseso ng pagmamanupaktura. Lalo na nagiging problema ang isyung ito sa mga susunod na yugto ng packaging at pagsubok, kung saan ang pagbabagu-bago ng temperatura at karagdagang mga mekanikal na stress ay maaaring maging sanhi ng mga microcrack na ito na mag-evolve sa mga nakikitang fracture, na posibleng humantong sa pagkabigo ng chip.
Upang mabawasan ang panganib na ito, mahalagang kontrolin nang mabuti ang proseso ng pagputol sa pamamagitan ng pag-optimize ng mga parameter tulad ng bilis ng pagputol, presyon, at temperatura. Ang paggamit ng hindi gaanong agresibong mga paraan ng pagputol, tulad ng laser dicing, ay maaaring mabawasan ang mekanikal na stress sa wafer at mabawasan ang pagbuo ng mga microcrack. Bukod pa rito, ang pagpapatupad ng mga advanced na paraan ng inspeksyon tulad ng infrared scanning o X-ray imaging sa panahon ng proseso ng wafer dicing ay makakatulong na matukoy ang mga maagang yugto na ito ng mga bitak bago sila magdulot ng karagdagang pinsala.
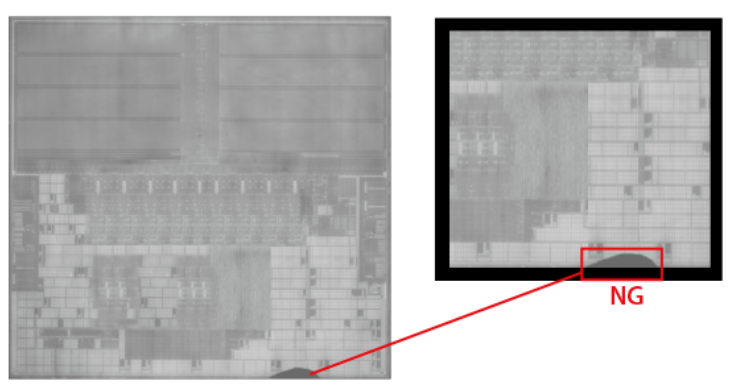
Ang pinsala sa ibabaw ng wafer ay isang makabuluhang alalahanin sa proseso ng dicing, dahil maaari itong magkaroon ng direktang epekto sa pagganap at pagiging maaasahan ng chip. Ang nasabing pinsala ay maaaring sanhi ng hindi wastong paggamit ng mga tool sa paggupit, hindi tamang mga parameter ng paggupit, o mga depektong materyal na likas sa wafer mismo. Anuman ang dahilan, ang mga pinsalang ito ay maaaring humantong sa mga pagbabago sa electrical resistance o capacitance ng circuit, na nakakaapekto sa pangkalahatang pagganap.
Upang matugunan ang mga isyung ito, dalawang pangunahing estratehiya ang sinusuri:
1.Pag-optimize ng mga tool sa paggupit at mga parameter: Sa pamamagitan ng paggamit ng mas matalas na mga blades, pagsasaayos ng bilis ng pagputol, at pagbabago sa lalim ng pagputol, ang konsentrasyon ng stress sa panahon ng proseso ng pagputol ay maaaring mabawasan, kaya binabawasan ang potensyal para sa pinsala.
2. Paggalugad ng mga bagong teknolohiya sa paggupit: Ang mga advanced na diskarte tulad ng laser cutting at plasma cutting ay nag-aalok ng pinahusay na katumpakan habang potensyal na binabawasan ang antas ng pinsala na naidulot sa wafer. Ang mga teknolohiyang ito ay pinag-aaralan upang makahanap ng mga paraan upang makamit ang mataas na katumpakan ng pagputol habang pinapaliit ang thermal at mekanikal na stress sa wafer.
Thermal Impact Area at ang mga Epekto Nito sa Performance
Sa mga proseso ng thermal cutting tulad ng laser at plasma cutting, ang mataas na temperatura ay hindi maiiwasang lumikha ng thermal impact zone sa ibabaw ng wafer. Ang lugar na ito, kung saan ang gradient ng temperatura ay makabuluhan, ay maaaring baguhin ang mga katangian ng materyal, na nakakaapekto sa panghuling pagganap ng chip.
Epekto ng Thermal Affected Zone (TAZ):
Mga Pagbabago sa Crystal Structure: Sa ilalim ng mataas na temperatura, ang mga atom sa loob ng materyal na wafer ay maaaring muling ayusin, na magdulot ng mga pagbaluktot sa istraktura ng kristal. Ang pagbaluktot na ito ay nagpapahina sa materyal, na binabawasan ang mekanikal na lakas at katatagan nito, na nagpapataas ng panganib ng pagkabigo ng chip sa panahon ng paggamit.
Mga Pagbabago sa Mga Katangian ng Elektrisidad: Maaaring baguhin ng mataas na temperatura ang konsentrasyon ng carrier at kadaliang kumilos sa mga materyal na semiconductor, na nakakaapekto sa electrical conductivity ng chip at kasalukuyang kahusayan ng transmission. Ang mga pagbabagong ito ay maaaring humantong sa isang pagbaba sa pagganap ng chip, na posibleng gawin itong hindi angkop para sa layunin nito.
Upang pagaanin ang mga epektong ito, ang pagkontrol sa temperatura sa panahon ng pagputol, pag-optimize sa mga parameter ng pagputol, at paggalugad ng mga pamamaraan tulad ng mga cooling jet o post-processing treatment ay mga mahahalagang diskarte upang mabawasan ang lawak ng thermal impact at mapanatili ang integridad ng materyal.
Sa pangkalahatan, ang parehong microcracks at thermal impact zone ay mga mahahalagang hamon sa teknolohiya ng wafer dicing. Ang patuloy na pagsasaliksik, kasama ng mga teknolohikal na pagsulong at mga hakbang sa pagkontrol sa kalidad, ay kinakailangan upang mapabuti ang kalidad ng mga produktong semiconductor at mapahusay ang kanilang pagiging mapagkumpitensya sa merkado.
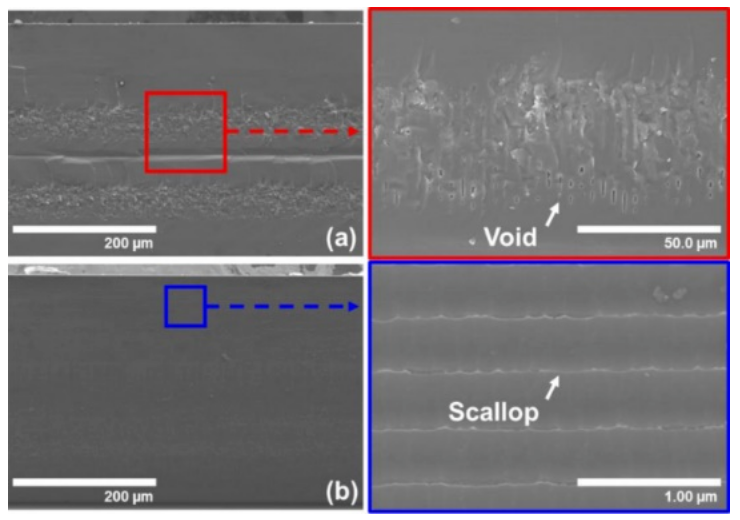
Mga Panukala upang Kontrolin ang Thermal Impact Zone:
Pag-optimize ng Mga Parameter ng Proseso ng Pagputol: Ang pagbabawas ng bilis ng pagputol at kapangyarihan ay maaaring epektibong mabawasan ang laki ng thermal impact zone (TAZ). Nakakatulong ito sa pagkontrol sa dami ng init na nabuo sa panahon ng proseso ng pagputol, na direktang nakakaapekto sa mga materyal na katangian ng wafer.
Advanced na Teknolohiya sa Paglamig: Ang paggamit ng mga teknolohiya tulad ng liquid nitrogen cooling at microfluidic cooling ay maaaring makabuluhang limitahan ang saklaw ng thermal impact zone. Ang mga paraan ng paglamig na ito ay nakakatulong sa pag-alis ng init nang mas mahusay, kaya pinapanatili ang mga materyal na katangian ng wafer at pinapaliit ang thermal damage.
Pagpili ng Materyal: Ang mga mananaliksik ay nag-e-explore ng mga bagong materyales, tulad ng carbon nanotubes at graphene, na nagtataglay ng mahusay na thermal conductivity at mekanikal na lakas. Maaaring bawasan ng mga materyales na ito ang thermal impact zone habang pinapabuti ang pangkalahatang pagganap ng mga chips.
Sa buod, kahit na ang thermal impact zone ay isang hindi maiiwasang kahihinatnan ng mga teknolohiya ng thermal cutting, maaari itong epektibong makontrol sa pamamagitan ng mga na-optimize na pamamaraan sa pagproseso at pagpili ng materyal. Ang hinaharap na pananaliksik ay malamang na tumutok sa fine-tuning at pag-automate ng mga proseso ng thermal cutting upang makamit ang mas mahusay at tumpak na wafer dicing.

Diskarte sa Balanse:
Ang pagkamit ng pinakamainam na balanse sa pagitan ng ani ng wafer at kahusayan sa produksyon ay isang patuloy na hamon sa teknolohiya ng wafer dicing. Kailangang isaalang-alang ng mga tagagawa ang maraming salik, tulad ng demand sa merkado, mga gastos sa produksyon, at kalidad ng produkto, upang makabuo ng makatuwirang diskarte sa produksyon at mga parameter ng proseso. Kasabay nito, ang pagpapakilala ng mga advanced na kagamitan sa pagputol, pagpapabuti ng mga kasanayan sa operator, at pagpapahusay ng kontrol sa kalidad ng hilaw na materyal ay mahalaga sa pagpapanatili o pagpapabuti ng ani habang pinapataas ang kahusayan sa produksyon.
Mga Hamon at Oportunidad sa Hinaharap:
Sa pagsulong ng teknolohiyang semiconductor, ang pagputol ng wafer ay nahaharap sa mga bagong hamon at pagkakataon. Habang lumiliit ang mga laki ng chip at tumataas ang pagsasama, ang mga pangangailangan sa katumpakan ng pagputol at kalidad ay lumalaki nang malaki. Kasabay nito, ang mga umuusbong na teknolohiya ay nagbibigay ng mga bagong ideya para sa pagbuo ng mga diskarte sa pagputol ng wafer. Ang mga tagagawa ay dapat manatiling nakaayon sa dynamics ng merkado at mga teknolohikal na uso, patuloy na pagsasaayos at pag-optimize ng mga diskarte sa produksyon at mga parameter ng proseso upang matugunan ang mga pagbabago sa merkado at mga teknolohikal na pangangailangan.
Bilang konklusyon, sa pamamagitan ng pagsasama-sama ng mga pagsasaalang-alang sa pangangailangan sa merkado, mga gastos sa produksyon, at kalidad ng produkto, at sa pamamagitan ng pagpapakilala ng mga advanced na kagamitan at teknolohiya, pagpapahusay ng mga kasanayan sa operator, at pagpapalakas ng kontrol sa hilaw na materyal, maaaring makamit ng mga tagagawa ang pinakamahusay na balanse sa pagitan ng ani ng wafer at kahusayan sa produksyon sa panahon ng pag-dicing ng wafer, na humahantong sa mahusay at mataas na kalidad na produksyon ng produktong semiconductor.
Outlook sa Hinaharap:
Sa mabilis na pag-unlad ng teknolohiya, ang teknolohiya ng semiconductor ay umuunlad sa hindi pa nagagawang bilis. Bilang isang kritikal na hakbang sa paggawa ng semiconductor, ang teknolohiya ng wafer cutting ay nakahanda para sa mga kapana-panabik na bagong development. Sa hinaharap, inaasahang makakamit ng teknolohiya ng paggupit ng wafer ang mga makabuluhang pagpapabuti sa katumpakan, kahusayan, at gastos, na nagbibigay ng bagong sigla sa patuloy na paglago ng industriya ng semiconductor.
Pagtaas ng Katumpakan:
Sa paghahangad ng mas mataas na katumpakan, ang teknolohiya ng pagputol ng wafer ay patuloy na itulak ang mga limitasyon ng mga kasalukuyang proseso. Sa pamamagitan ng malalim na pag-aaral ng mga pisikal at kemikal na mekanismo ng proseso ng paggupit at tumpak na pagkontrol sa mga parameter ng paggupit, ang mas pinong mga resulta ng pagputol ay makakamit upang matugunan ang lalong kumplikadong mga kinakailangan sa disenyo ng circuit. Bukod pa rito, ang paggalugad ng mga bagong materyales at mga paraan ng pagputol ay makabuluhang mapapabuti ang ani at kalidad.
Pagpapahusay ng Kahusayan:
Ang bagong kagamitan sa paggupit ng wafer ay tututuon sa matalino at automated na disenyo. Ang pagpapakilala ng mga advanced na sistema ng kontrol at mga algorithm ay magbibigay-daan sa kagamitan na awtomatikong ayusin ang mga parameter ng paggupit upang mapaunlakan ang iba't ibang mga materyales at mga kinakailangan sa disenyo, kaya makabuluhang pagpapabuti ng kahusayan sa produksyon. Ang mga inobasyon tulad ng multi-wafer cutting technology at mabilis na pagpapalit ng blade system ay gaganap ng mahalagang papel sa pagpapahusay ng kahusayan.
Pagbawas ng mga Gastos:
Ang pagbabawas ng mga gastos ay isang pangunahing direksyon para sa pagbuo ng teknolohiya ng paggupit ng wafer. Habang nabuo ang mga bagong materyales at paraan ng pagputol, inaasahang mabisang makokontrol ang mga gastos sa kagamitan at mga gastos sa pagpapanatili. Bukod pa rito, ang pag-optimize sa mga proseso ng produksyon at pagbabawas ng mga scrap rate ay higit na makakabawas sa basura sa panahon ng pagmamanupaktura, na humahantong sa pagbaba sa kabuuang gastos sa produksyon.
Smart Manufacturing at IoT:
Ang pagsasama-sama ng matalinong pagmamanupaktura at mga teknolohiya ng Internet of Things (IoT) ay magdadala ng mga pagbabago sa pagbabago sa teknolohiya ng pagputol ng wafer. Sa pamamagitan ng interconnectivity at pagbabahagi ng data sa pagitan ng mga device, ang bawat hakbang ng proseso ng produksyon ay maaaring masubaybayan at ma-optimize sa real time. Ito ay hindi lamang nagpapabuti sa kahusayan sa produksyon at kalidad ng produkto ngunit nagbibigay din sa mga kumpanya ng mas tumpak na pagtataya sa merkado at suporta sa paggawa ng desisyon.
Sa hinaharap, ang teknolohiya ng pag-cut ng wafer ay gagawa ng kapansin-pansing pag-unlad sa katumpakan, kahusayan, at gastos. Ang mga pagsulong na ito ay magtutulak sa patuloy na pag-unlad ng industriya ng semiconductor at magdadala ng higit pang mga makabagong teknolohiya at kaginhawahan sa lipunan ng tao.
Oras ng post: Nob-19-2024